DAkkS-DKD calibration
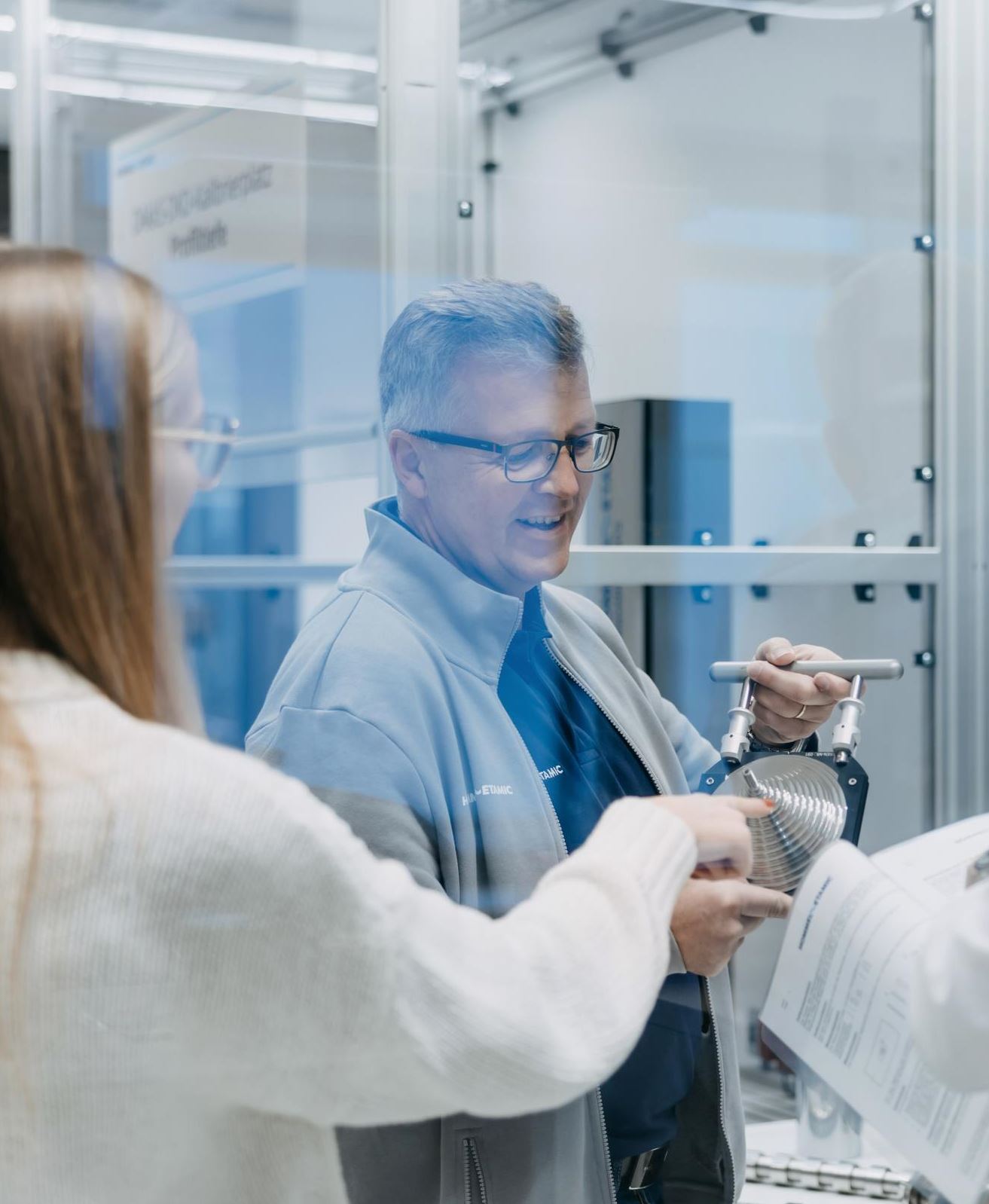
It is extremely important to continuously monitor the measuring systems used to ensure the best possible measurement accuracy for seamless quality assurance. This is because only calibrated measuring devices ensure that meaningful and correct results can be obtained.
Constantly taking measurements and the resulting wear and tear can alter the accuracy of the measurement without this being noticed. Therefore, the measuring devices must be regularly calibrated with traceable standards.
We calibrate your standards and entire measuring systems in our DKD calibration laboratory accredited by the German Accreditation Body (DAkkS) in accordance with ISO/IEC 17025 -– or on your premises, if you wish. By tracing the measuring equipment and the standards directly back to the German Metrology Institute (PTB), you can rest assured that the equipment's measuring capability, and obtain measurements and calibrations of the utmost metrological standard.
The benefits for you
- Proof of measuring device reliability
- Compliance with standards, guidelines and certifications
- Your standards and measurements can be directly traced to national standards
- International recognition
- Statement of measurement uncertainty
- Audit-acceptable certificates
- Trust in and credibility of the accuracy of the measurement results
- Process security
DAkkS-DKD calibrations are the perfect solution for users of measuring equipment who require a particular level of safety, accuracy and reliability.
Certified in accordance with
ISO 17025
Internationally recognized
ILAC certification
Reliable results
Traceability to national standards
- DAkkS accredited DKD calibration laboratory
- Calibration services & standards
- Standards, guidelines & literature
- PTB, DKD, DAkkS
- Glossary
DAkkS accredited DKD calibration laboratory
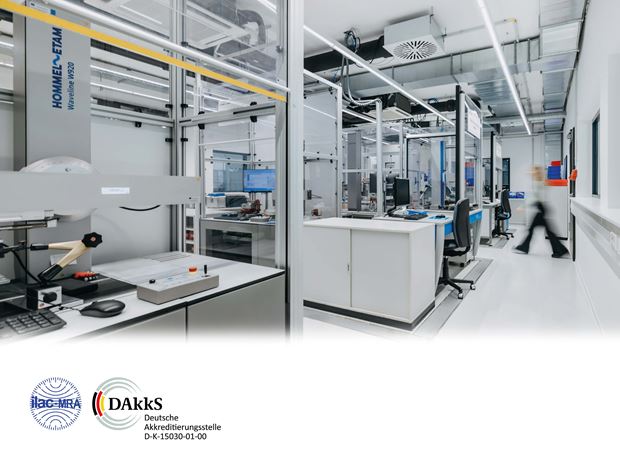
The DKDcalibration laboratory, D-K-15030-01-00 of JENOPTIK Industrial Metrology Germany GmbH, has been accredited by the German Accreditation Body (DAkkS) in accordance with ISO/IEC 17025 since 1980. The laboratory works independently and has standards that have been set and calibrated by the National Metrology Institute (PTB).
Every single measurement on unknown standards and measurement devices is related to this reference standards, and can therefore be traced back to national standards in accordance with ISO 9000. This is confirmed by the internationally recognized DAkkS-DKD calibration certificate that comes under the ILAC agreement.
To ensure that the systems used to take the measurements produce correct and coherent results, they have to be regularly checked by an accredited calibration laboratory, so they can be traced back to national standards. You can therefore rest assured that the measured values are accurate and that measurement uncertainties are especially small.
Scope of accreditation
The scope of accreditation of our DKD calibration laboratory has been successively extended since the initial accreditation in 1980. Our scope of accreditation currently includes the following variables:
- Roughness – including ISO 21920
- Depth setting standards
- Surface profilers (roughness measuring devices)
- Form standards
- Contour standards
- Cam standards
- Shaft measuring devices (Opticline)
Download the DAkkS accreditation scope
How often should measuring devices be calibrated?
The frequency of calibration is not laid down, and may vary from one month to several years. It depends on the following factors:
- the change of device components
- the frequency of use
- the uncertainty requirements of the measuring device
- the stability of the measuring device
If wear is noticed, or if damage is suspected, a recalibration should be carried out immediately. With short calibration periods, the user can increase the average quality.
DAkkS accredited DKD calibration laboratory | Chronology
Since the initial accreditation of our calibration laboratory in 1980, we have been constantly extended our range of services.
- 1977 | Founding of the German Calibration Institute (DKD) by the German federal ministry for the economy, the Federal association of German Industry (BDI) and the German Metrology Institute (PTB)
- 1978 | Hommelwerke GmbH submitted its application to set up a DKD calibration site
- 1980 | On September 23, Hommelwerke GmbH, received as one of the first 30 companies, the confirmation certificate to operate a calibration site (DKD 2401) for the roughness parameters Rmax, Rz and Ra
- 1992 | The scope of accreditation was extended to groove depth Pt
- 1994 | The services were extended again to include the roughness parameters Rpk, Rk, Rvk, Mr1 and Mr2, groove depth Pt to 100 µm; and measurement uncertainties were reduced for Rmax, Rz and Ra
- 1996 | Third extension to the surface profilers and reduction of the measurement uncertainty for Pt
- 2002 | The services were extended for a fourth time to include the roughness parameter RSm, roughness parameters in accordance with SEP 1940, the measurement uncertainties Rmax, Rz and Ra were reduced; accreditation was obtained for form parameters, roundness deviation, roundness flick standards, straightness deviation and parallelism deviations
- 2008 | The services were extended to include contour characteristics for contour standards: lateral distances, vertical distances, radii and angles
- 2010 | Accreditation was switched from DKD to DAkkS. The sixth extension to services was made to include superfine roughness standards and to reduce measurement uncertainties for all contour characteristics
- 2015 | Seventh extension to include cam standards with 14 different characteristics
- 2023 | Eighth extension for depth setting standards up to 5,500 for depth, roughness parameters according to ISO 21920, shaft measuring devices and measurement uncertainty reduction for roughness measurements and roundness deviation
Strict requirements for reliable results
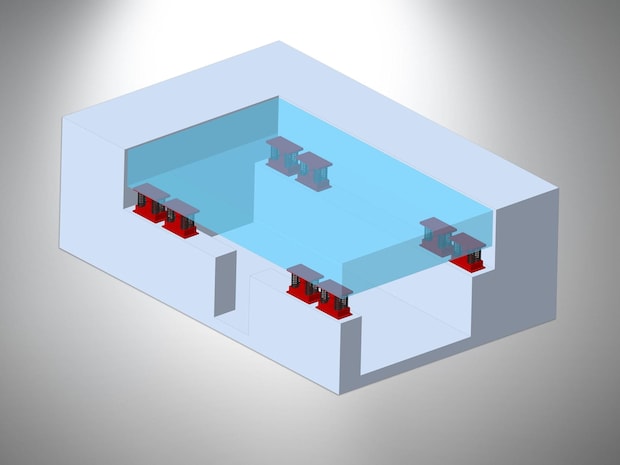
Vibration minimization thanks to spring elements in the foundation
Our DAkkS accredited DKD calibration laboratory is operated in accordance with strict quality benchmarks in a climate-controlled and vibration-minimized measurements room.
Accredited experts regularly carry out on-site monitoring visits during which the material and specialist personnel must provide evidence of their suitability.
Calibration services and & standards
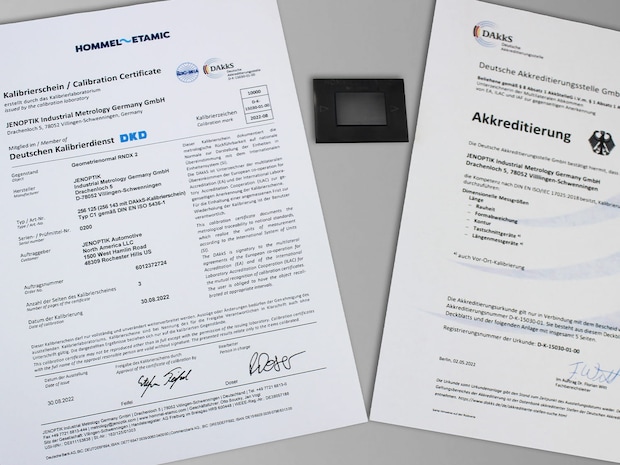
Our DAkkS accredited DKD calibration laboratory issues DAkkS-DKD calibration certificates for roughness, form, contour and cam standards. Shaft measuring devices and surface profilers for measuring roughness – including on site, at the client's premises – can be calibrated to DAkkS-DKD standards. The calibration certificate documents the condition of the measuring device at the time of calibration.
DAkkS-DKD measurements are taken with the standards that are prescribed by and traced to the PTB. This ensures that the measurement results are uniform and independent. If a standard cannot be calibrated, you can obtain new standards from us.
For some calibrations, no DAkkS accreditation is currently possible, for example for roughness measuring systems with skid probes or for measuring devices. We do, however, also offer high-quality calibration services for these. Our trained staff use only standards that can be traced back to international SI units.
For non-accredited parameters or as less expensive alternatives, we issue factory calibration certificates or factory test reports. For calibrations that do not come under the area of expertise of our calibration laboratory, we also work with selected external DAkkS-DKD calibration laboratories.
DAkkS-DKD calibration certificate
- Unique reference number
- Short description of the measurement procedure
- Reference standards used
- Standards applied (ISO...)
- Representation of the measurement results with their corresponding measurement uncertainties
DAkkS-DKD calibration certificates are internationally recognized as part of the ILAC agreement (International Laboratory Accreditation Cooperation).
Calibration services for standards
Roughness standards
DAkkS-DKD calibration certificates for roughness standards
JENOPTIK Industrial Metrology Germany GmbH exhibits the smallest DAkkS accredited measurement uncertainties for roughness measurements.
Your standards are calibrated at our DAkkS-DKD measuring station in an air-conditioned and vibration-minimized precision measuring room using the stylus method. Standards that are traced to and prescribed by the PTB are used for this. The DAkkS accredited roughness depths are situated for various roughness values between 0.015 µm and 20 µm. Your calibrations are carried out in accordance with ISO 4287/13565 and, as an option, in accordance with the new standard series ISO 21920.
Roughness standards are used for the entire calibration and for checking roughness measuring devices. The two most common types are geometry standards and roughness standards.
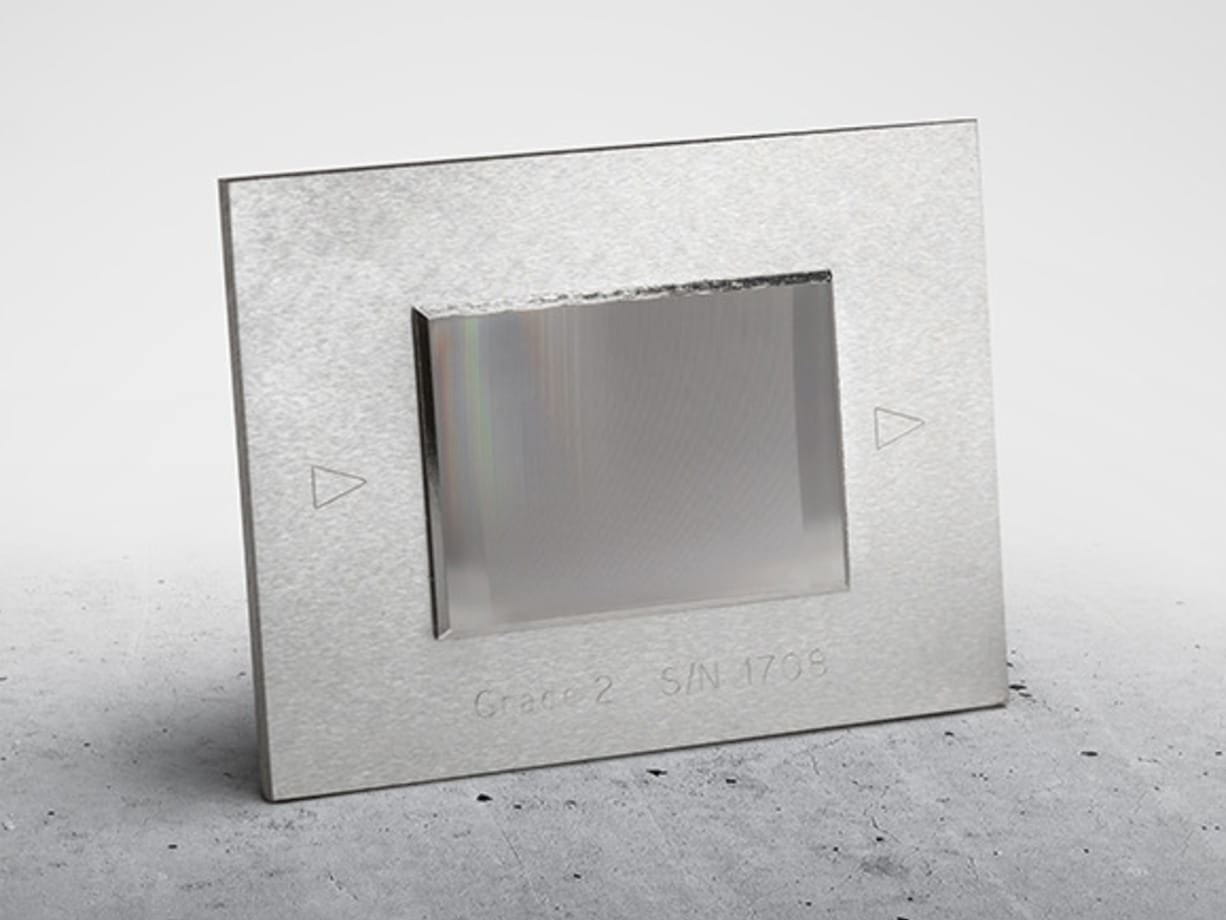
Geometry standards
- Type C (ISO 5436-1)
- Calibration in accordance with ISO 4287 or ISO 21920
- Calibration and adjustments of vertical magnification, horizontal profile measurement, the uniformity of the traverse function and the transmission function of the roughness measuring system
- Periodic, regular sine-wave profile structure
- Extremely practice-oriented and simple to use
- Mostly large measurement surfaces, very homogeneous and repeatable, and consequently low measurement uncertainties
- Reasonably priced
- The hard coated models are very suitable for skid measurements
- Calibration values: Rmax, Rzx, Rz, Ra, RSm
- With a DAkkS-DKD calibration certificate
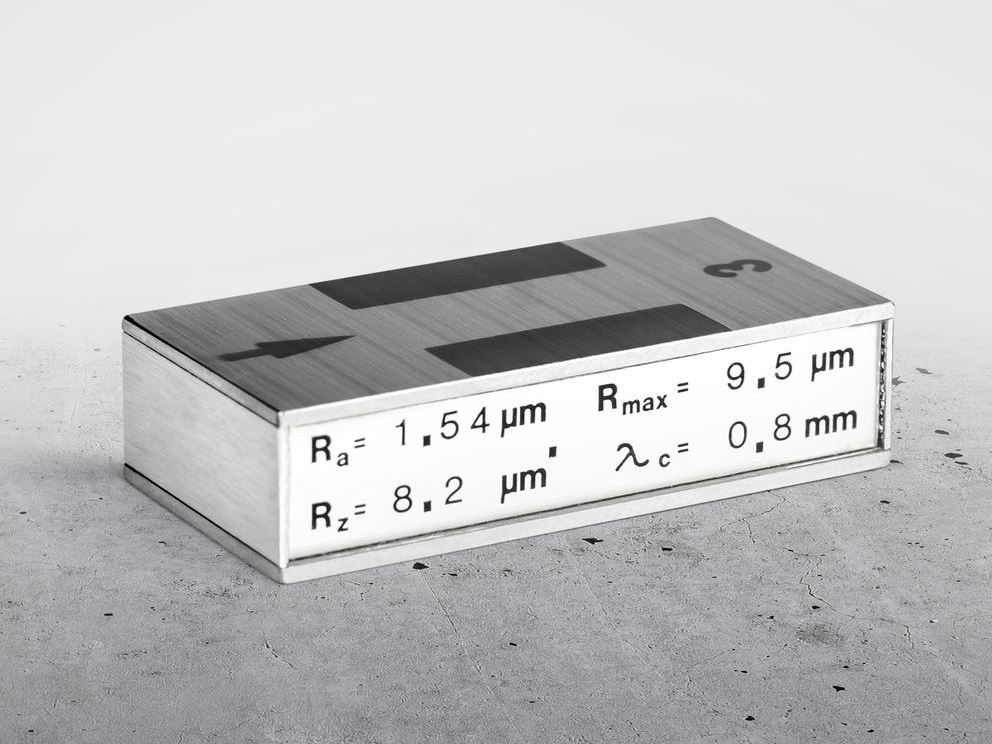
Roughness standards
- Type D (ISO 5436-1)
- Calibration in accordance with ISO 4287 and ISO 13565 or ISO 21920
- Calibration of the roughness measuring system, verification of the correct settings of the cut-off and the type of wave filter
- Acyclic, irregular surface profile which is modeled on practice.
- Surface deviations such as waviness and roughness with various amplitudes, cut-offs and phase lengths
- Calibration values: Rmax, Rzx, Ra, Rk, Rpk, Rvk, Mr1, Mr2, Rmrk1, Rmrk2
- With a DAkkS-DKD calibration certificate
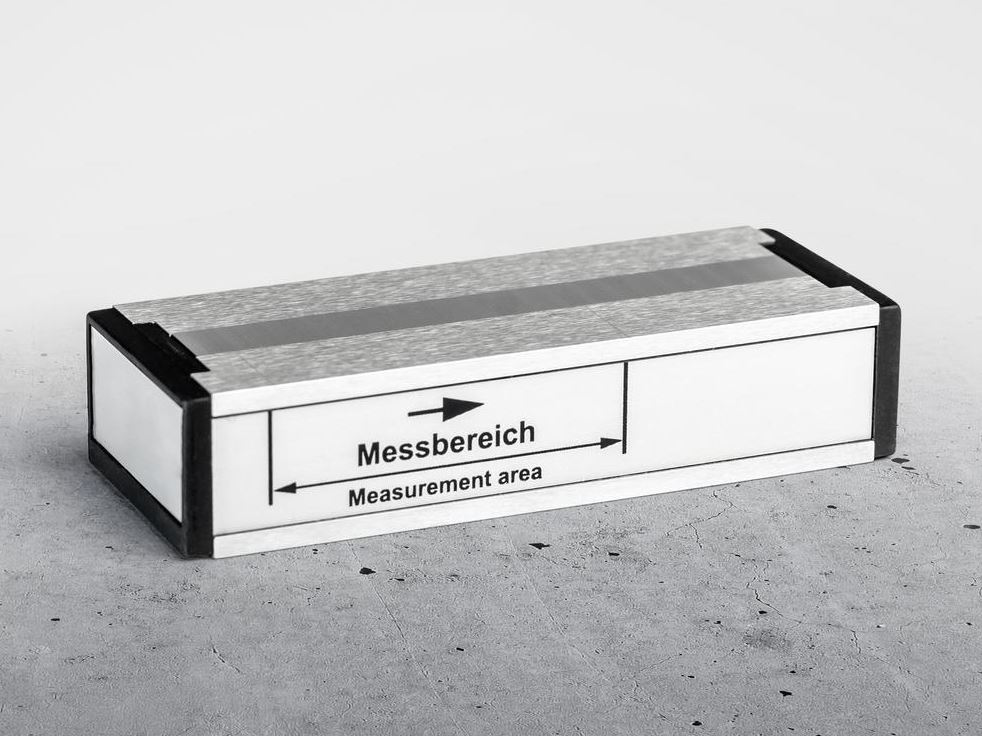
Sheet metal standards
- Type D (ISO 5436-1)
- Calibration in accordance with EN 10049 and SEP 1940
- Calibration and verification of the roughness measuring system for parameters in accordance with EN 10049 or steel-iron-test sheet SEP 1940 that are measured with a dual-skid pick-up probe
- Aperiodic, irregular profile structure without disrupting waviness or outliers (peaks)
- Calibration values: Rz, Ra, RPc
- With a DAkkS-DKD calibration certificate
Summary of standards and services
Depth setting standards
DAkkS-DKD calibration certificates for depth setting standards
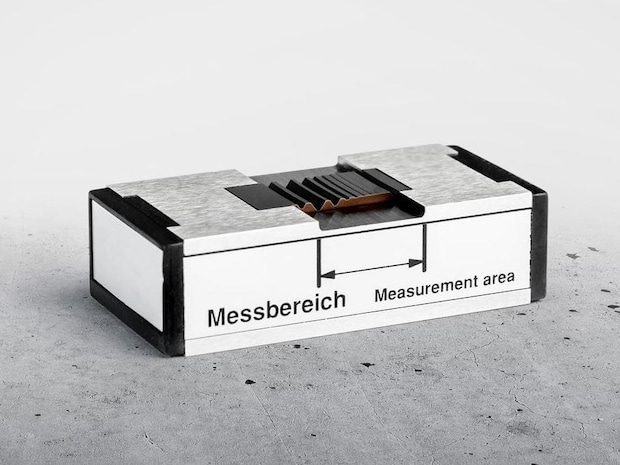
In the area of depth setting standards, JENOPTIK Industrial Metrology Germany GmbH has the smallestDAkkS accredited measurement uncertainties and the largest measurement range (up to 5,500 µm).
Your standards are calibrated at our DAkkS-DKD measuring station in an air-conditioned and vibration-minimized precision measuring room using the stylus method. Standards that are traced to and prescribed by the PTB are used for this. The DAkkS accredited depths fall within the range of 0.15 µm to 5,500 µm. The Pt value is calibrated in accordance with ISO 4287 or ISO 21920, and the d value in accordance with ISO 5436-1.
Depth setting standards
- Type A (ISO 5436-1)
- Calibration in accordance with ISO 4287 or ISO 5436-1
- Calibration values Pt or d
- Calibration and adjustment of the vertical magnification and the determination of repeatability of roughness measuring systems
- Very homogeneous and consequently reproducible
- Very small measurement uncertainties
- Directly traced back to the SI unit
- Worldwide only accredited laboratory for depths of up to 5,500 µm
- Measurement uncertainty ≥ 0.012 µm
- With a DAkkS-DKD calibration certificate
Summary of standards and services
Form standards
DAkkS-DKD calibration certificates for form standards
Your form standards are calibrated on our DAkkS-DKD measuring station in an air-conditioned and vibration minimized fine-measurement room with a rotating spindle measuring system with measuring Z axis. All common form parameters can be determined.
We distinguish between two types of device for our Formline measuring systems: The classic roundness and form measuring devices for determining form and positional characteristics, for which the workpiece is adapted to the rotation axis, and shaft measuring systems for checking camshafts and crankshafts with workpiece clamping between points and additional determination of dimensional characteristics.
Standards for roundness and form measuring devices
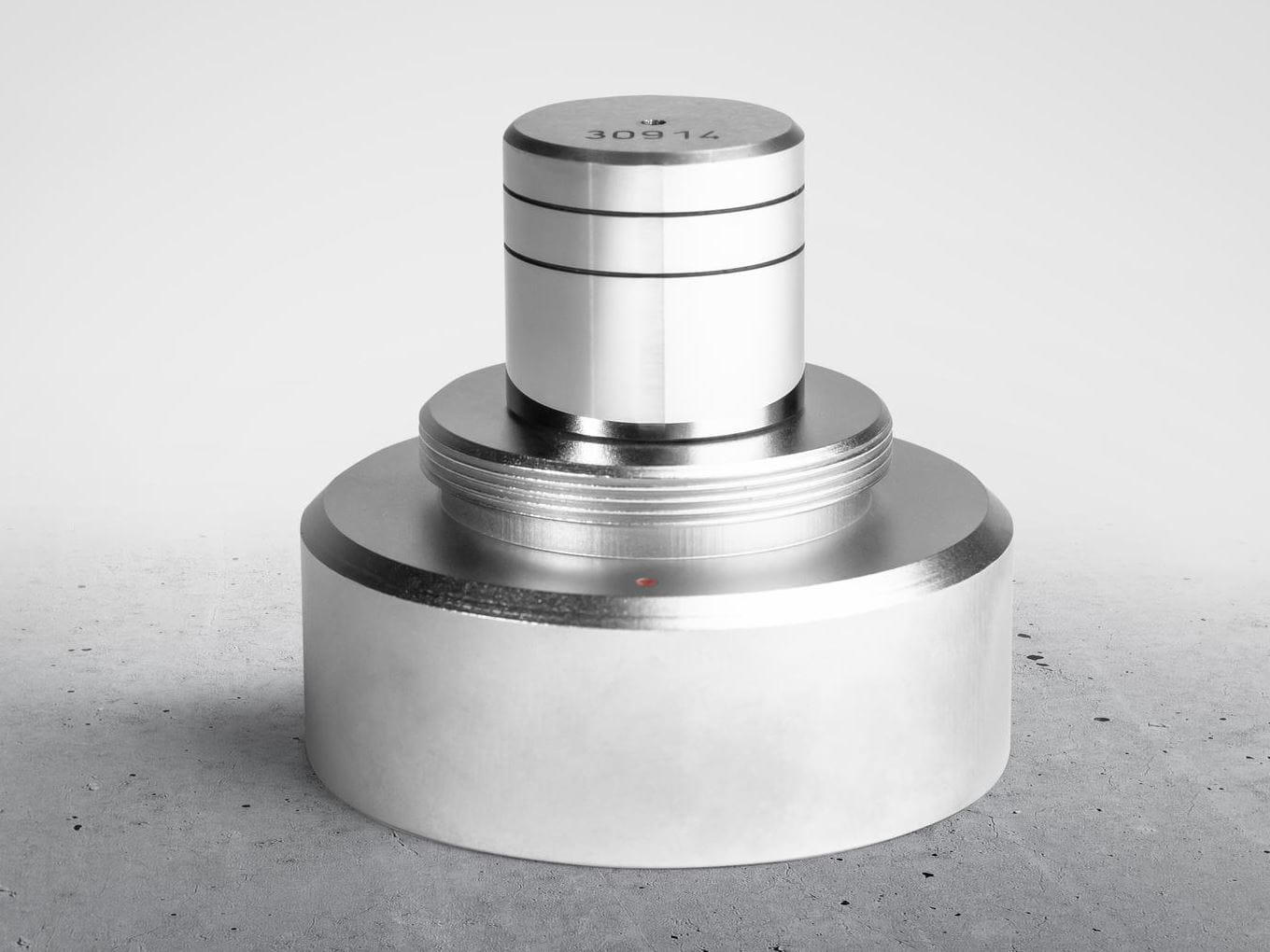
Magnification standards
- Calibration in accordance with ISO 12181-1, DAkkS-DKD-R 4-4
- Magnification or flick standards are used to dynamically check or adjust the vertical magnification of the measuring device
- It is a precision cylinder on which the flatness (flick) is marked, the depth of which is calibrated in the form of a roundness deviation
- It is made from stainless steel and is therefore resistant to wear and corrosion
- Determining roundness deviations for all current wave filters
- Measurement uncertainty ≥0.1 µm
- With a DAkkS-DKD calibration certificate
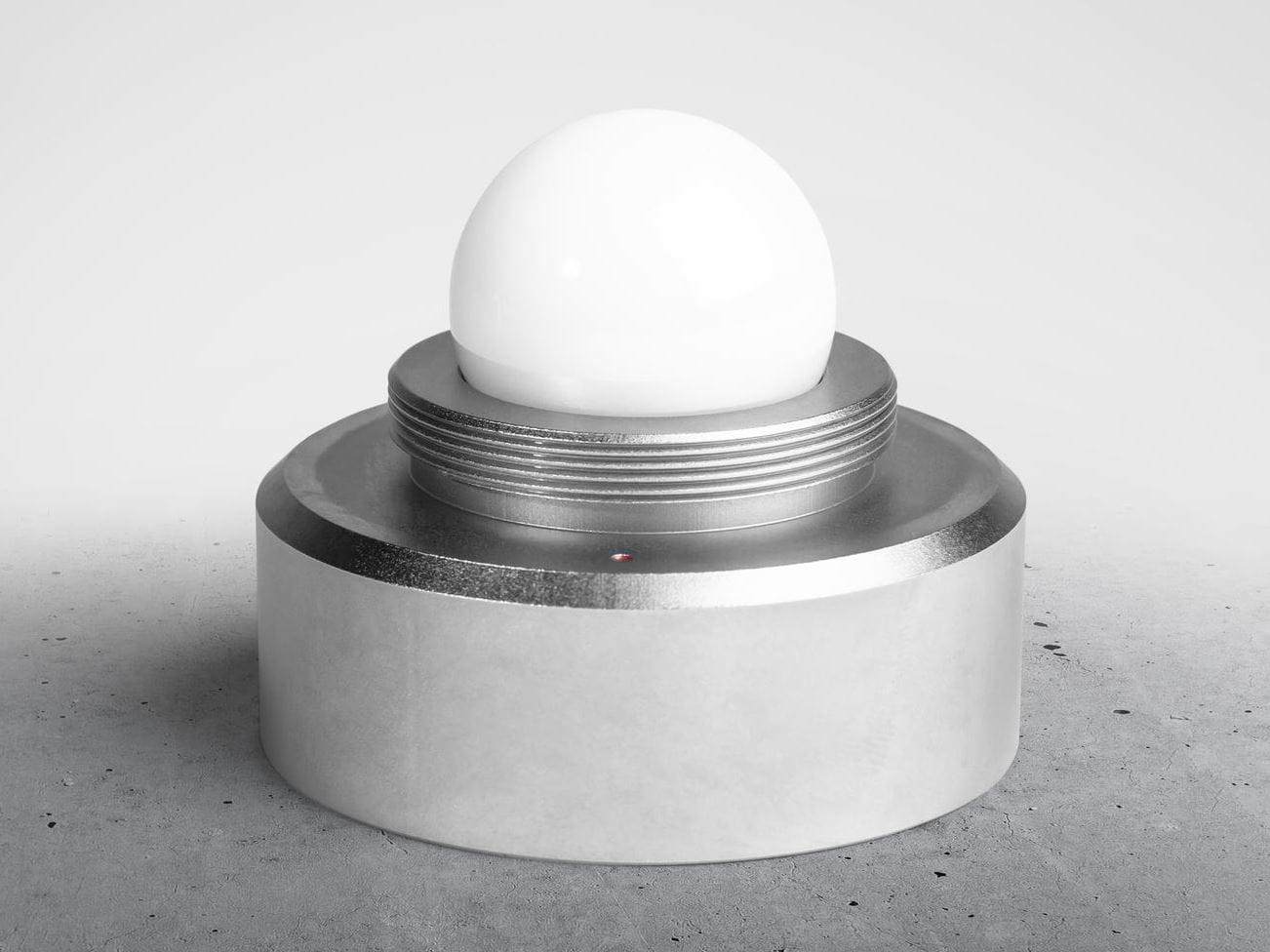
Roundness standards
- Calibration in accordance with ISO 12181-1, DAkkS-DKD-R 4-4
- Roundness standards comprise a precision sphere
- They are used to check or adjust the rotary guide deviation (C axis) of the form or roundness measuring devices
- They are made from ceramic and, therefore, extremely resistant to wear and are long-lasting
- Determining roundness deviations for all current wave filters
- Roundness error ≤0.03 µm
- Measurement uncertainty ≥0.025 µm
- With a DAkkS-DKD calibration certificate
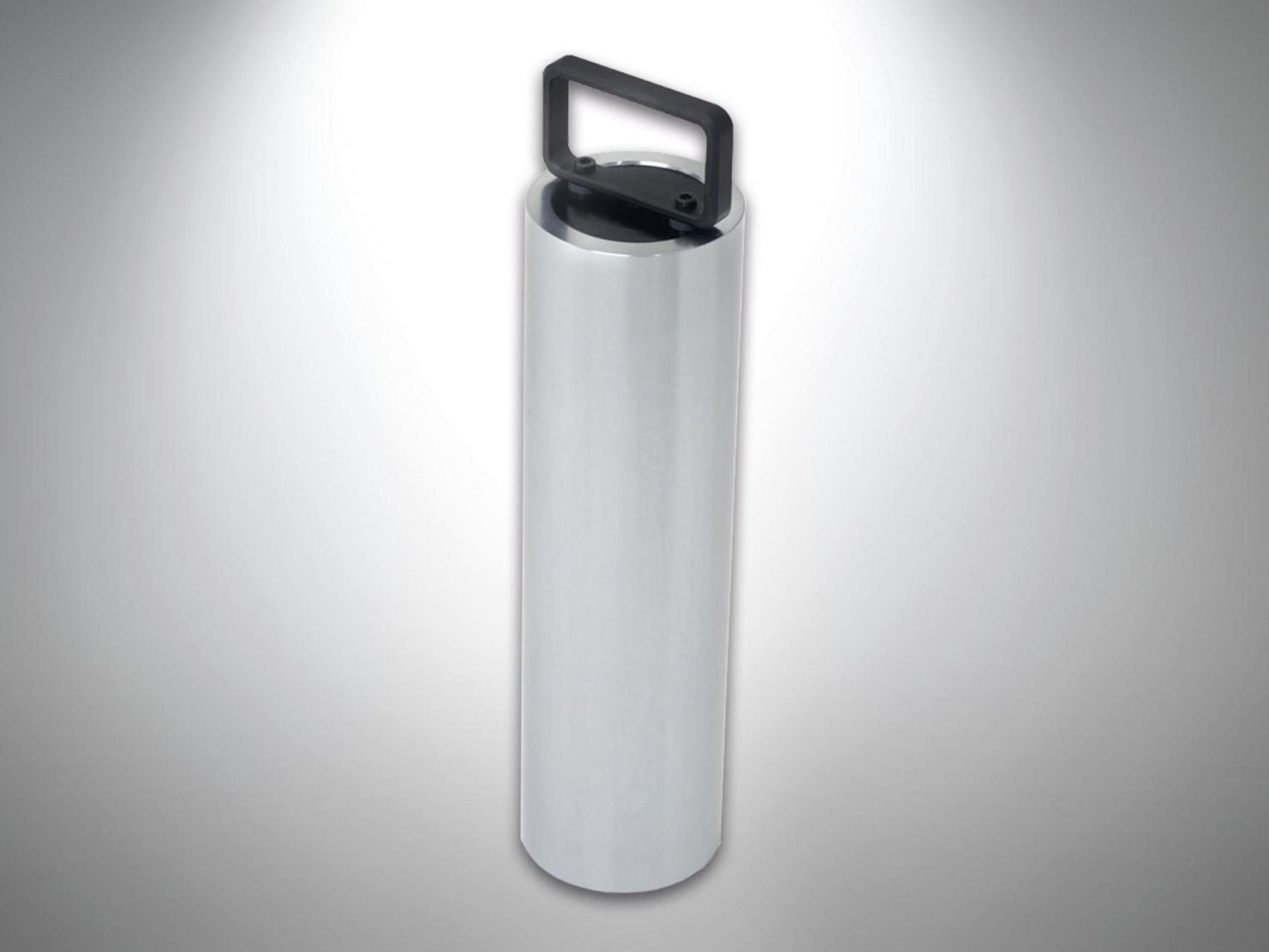
Measurement columns | Cylinders
- Calibration in accordance with ISO 12181-1, DAkkS-DKD-R 4-4
- Multifunction standard for checking and partly adjustment of form or roundness measuring devices
- Made from a corrosion-free precision cylinder
- Calibrated characteristics: roundness, straightness, parallelism, levelness and cylinder form deviation
- The Swiss state institute, METAS (similar to the PTB) carries out the calibration based on very small measurement uncertainties
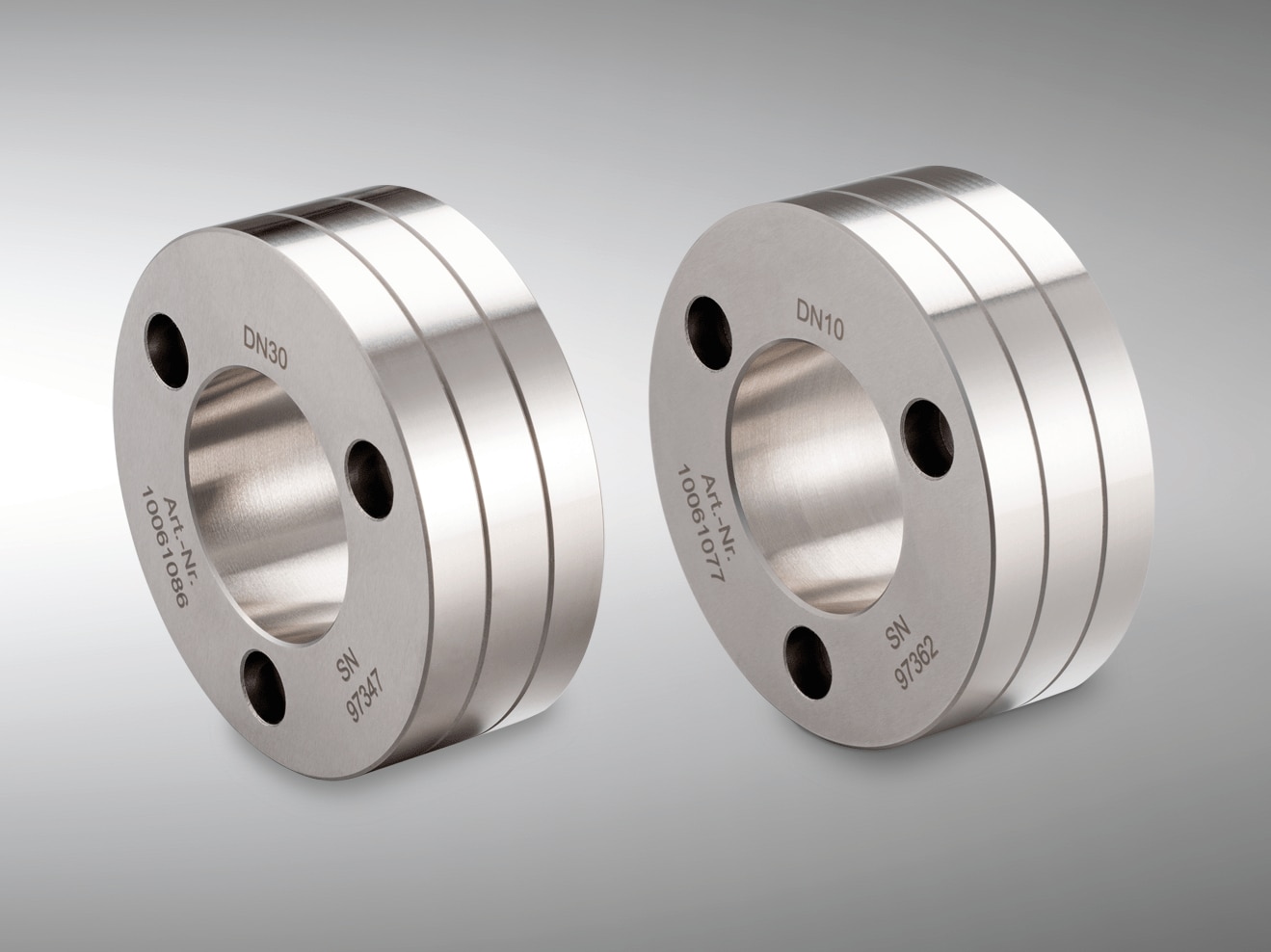
Twist standards
- Calibration in accordance with MBN 31 007-7
- To determine twist characteristics in accordance with the technical standard MBN 31 007-7
- Three-dimensional recording of the cylinder surface and evaluation of the characteristics for tightness for dynamically stressed radial shaft seals
- Rust-free steel cylinders with a special multi-thread twist profile ground into the outer surface
- Determination of the twist characteristics DG, DP, Dt and DF
- Delivered as a set comprising a standard with 10 threads (DN10) and a standard with 30 threads (DN30)
- With a factory calibration protocol, since there are no DAkkS accredited laboratories for twist characteristics

Single wave standards
- Calibration in accordance with ISO 12181-1
- For dynamic testing of the sensitivity of a form measuring device and for filter testing using the Fast Fourier Transformation (FFT)
- Cylinder into which a sine-wave shaped profile with 500 waves is integrated
- Determination of the roundness deviations for all common wave filters and the amplitude height H500
- With a factory calibration certificate, since there is no approved DAkkS accredited laboratory for carrying out Fast Fourier Transformations
Standards for camshaft and crankshaft measuring systems

Camshaft standards
- Calibration in accordance with ISO 15530-3
- Multifunction standard for checking or calibrating a camshaft measuring device
- Modeled on a conventional camshaft, consisting of three main bearing points (L1, L2 and L3), two cams (N1 and N2) and two eccentric circular disks (Ex1 and Ex2), which represent the cam lift
- Assessment of form and dimensional deviations of all kinds of measurements: Cam form, cam pitch, cam height and width, cam base circle radius and run-out, cam angle, diameter, roundness, straightness, parallelism and cylindricity
- With a factory calibration certificate, since the PTB cannot provide the necessary traceability at the moment to the required level of precision
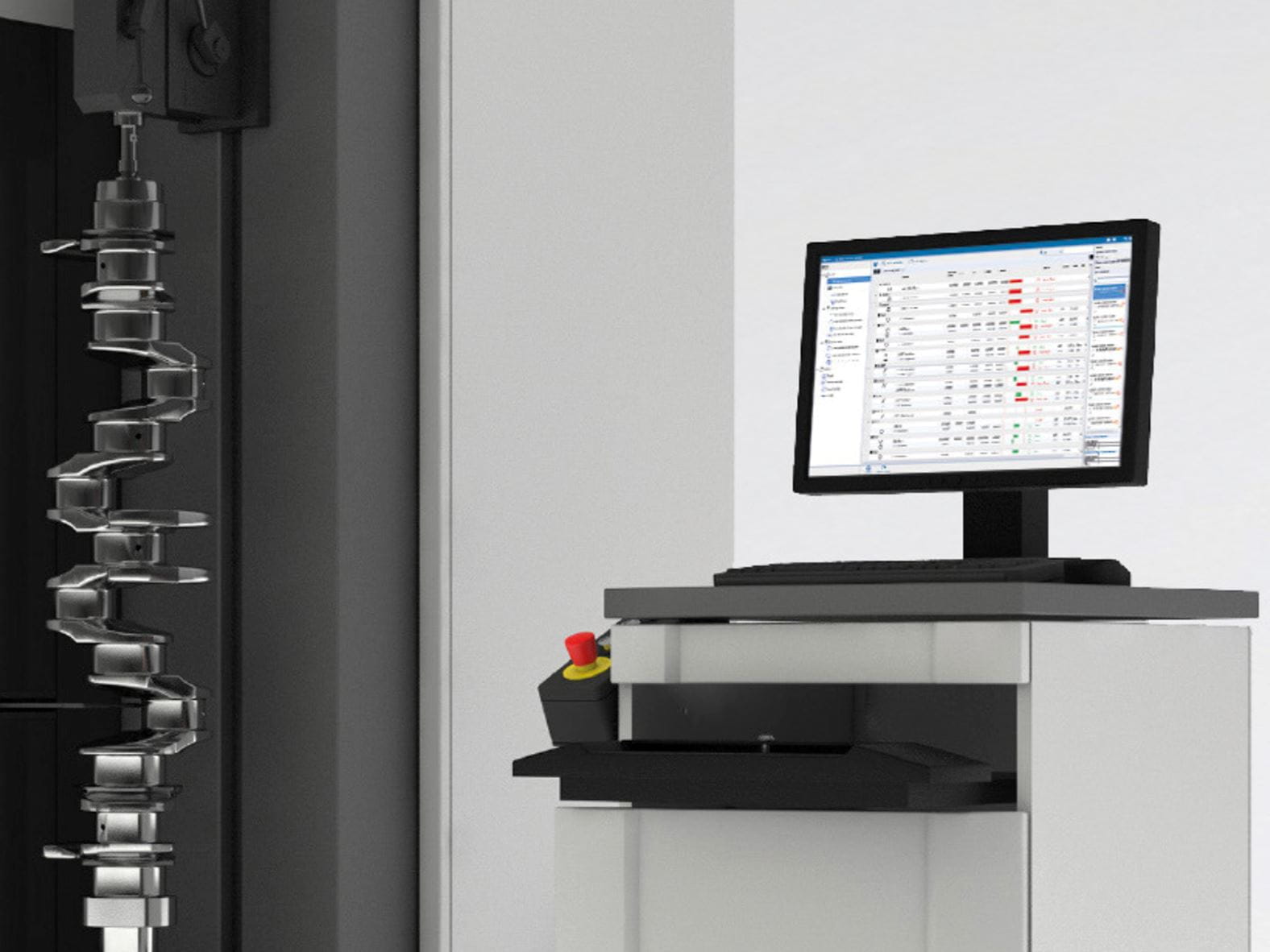
PTB-certified evaluation software Tolaris Shaft
- Evaluation algorithms validated by the PTB to compare evaluation strategies and to take into account the effect of software, without considering the purely mechanical measurement process
- Measurement uncertainty is determined used synthetic reference data
- Certified software measurement uncertainty

Crankshaft standards | System controllers
- Calibration in accordance with ISO 12181-1, DAkkS-DKD-R 4-4
- To check or calibrate a crankshaft measuring device
- Modeled on a crankshaft, consisting of two eccentrics and two bearing points
- With a factory calibration certificate for the following form and position deviations: Roundness, straightness, parallelism, cylindricity and axial run-out
- Other DAkkS-DKD calibrations can be subcontracted to external calibration laboratories for the dimensional characteristics of diameter, lengths and angles
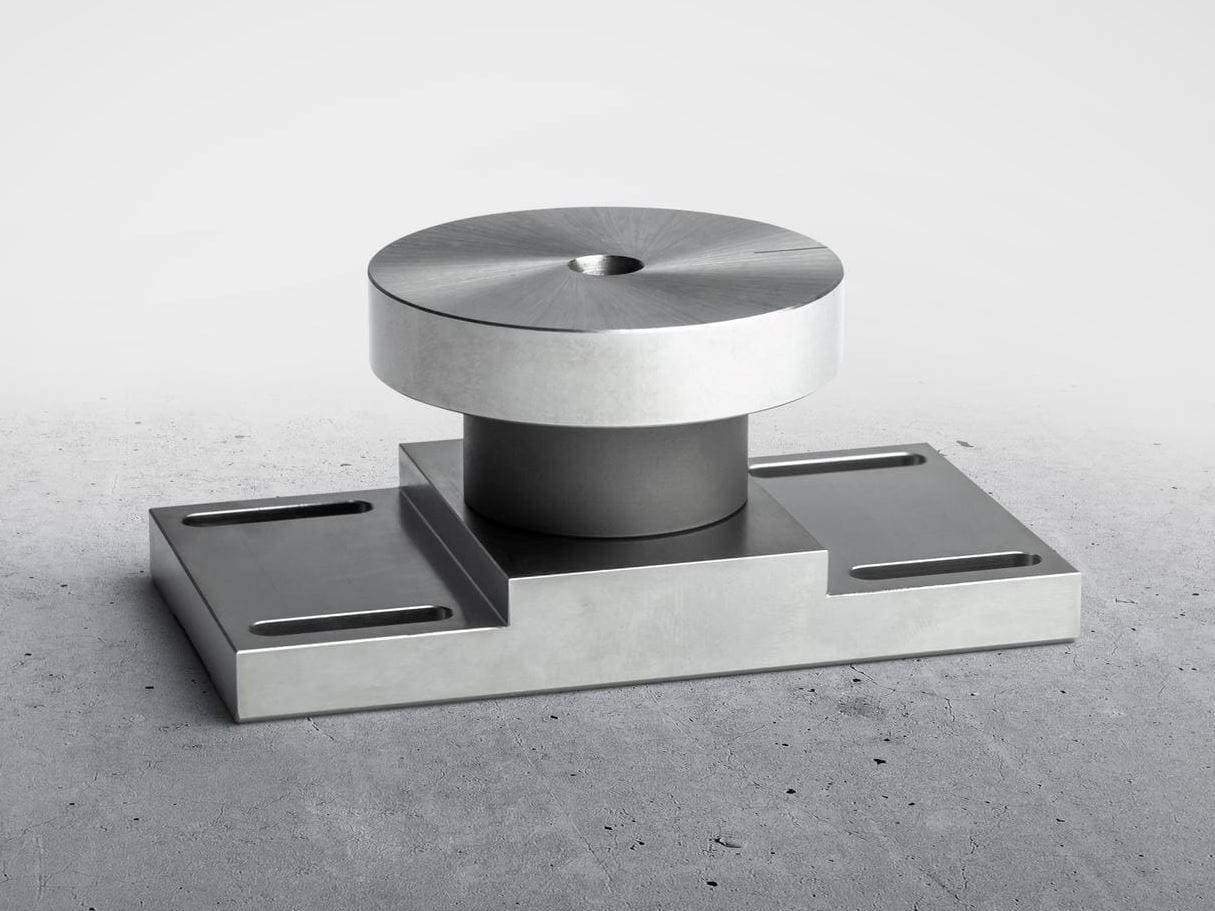
Roundness standards | Testing device
- Calibration in accordance with ISO 12181-1, DAkkS-DKD-R 4-4
- Checking or calibrating of roundness errors
- Centric and eccentric fixation in a crankshaft measuring machine
- Comprising highly precise, hardened and non-corrosive cylinder disks
- With a DAkkS-DKD calibration certificates for roundness deviations
Summary of standards and services
Contour standards
DAkkS-DKD calibration certificates for contour standards

Contour standard KN8
- Calibration according to ISO 15530-3 and VDI/VDE 2629-1
- To check or calibrate a contour measuring system
- Multifunctional standard with which the following characteristics can be checked: Distances (in X and Z direction), radii (convex and concave) and angles (exterior and interior)
- Made from hard metal therefore non-corrosive
- Constant profile form in transverse direction
- With a DAkkS-DKD calibration certificate
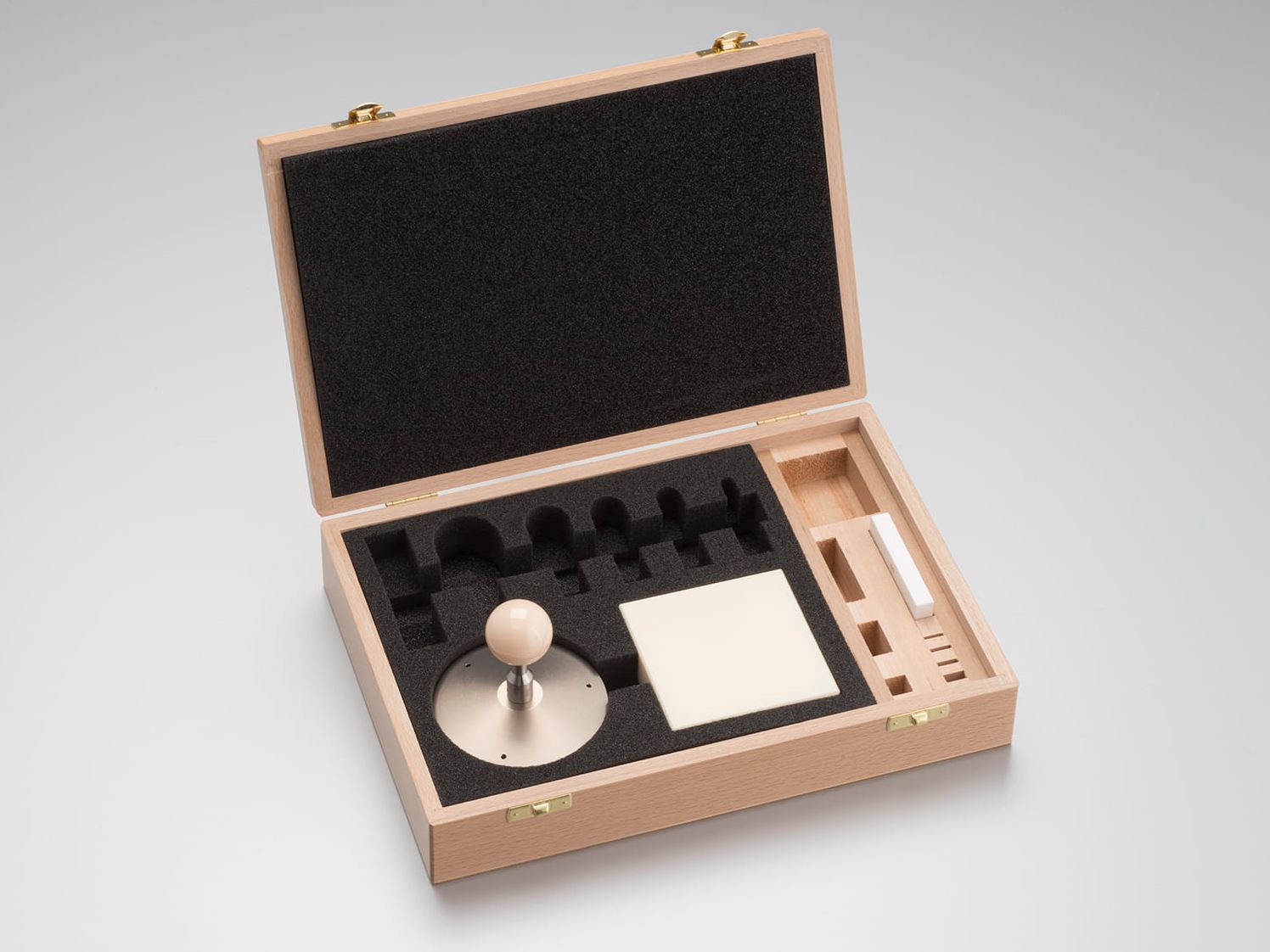
Calibration sets
Calibration sets consist of calibration balls and calibration gage blocks that are used to adjust the measuring device and calibrate the probe arms.
- Calibration in accordance with the KMG two point procedure or VDI/VDE/DGQ 2618-1
- Calibration balls with various diameters, regardless of the contour measuring device used; they are made from ceramic or ruby, and are, therefore, resistant to wear and are extremely precise
- Calibration gage blocks with different heights, according to the contour device used; they are made from ceramic or hard metal, and are, therefore, resistant to wear and corrosion
- DAkkS-DKD calibration is carried out at an external calibration laboratory
Summary of standards and services
Opticline standards
DAkkS-DKD calibration certificates for Opticline standards
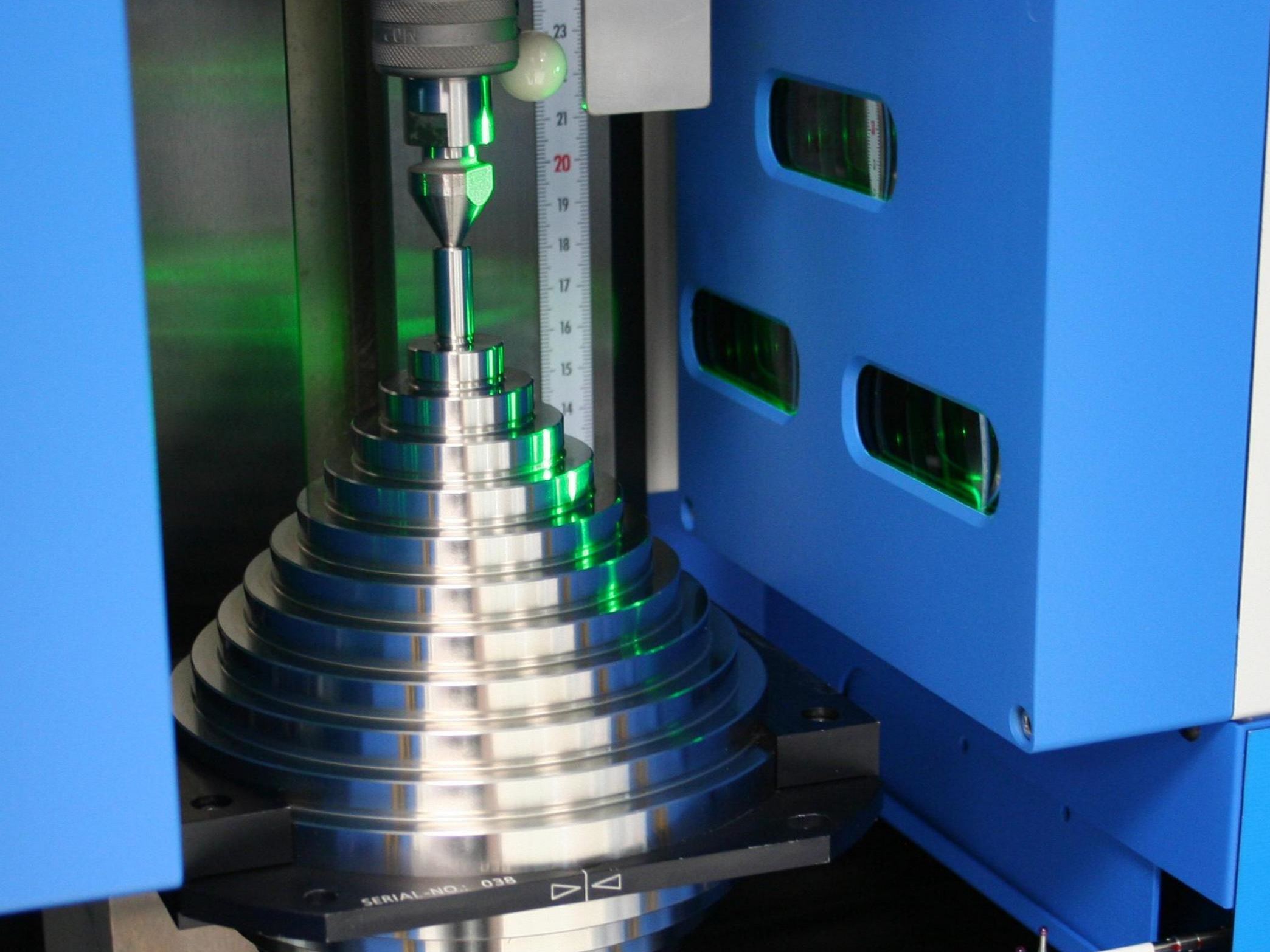
Step masters
- To check or calibrate the image processing system in the direction of rotation
- Comprising several cylinder disks with various diameters; the maximum disk diameter is based on the measurement range of the Opticline machine to be checked
- DAkkS-DKD calibration is carried out at an external calibration laboratory
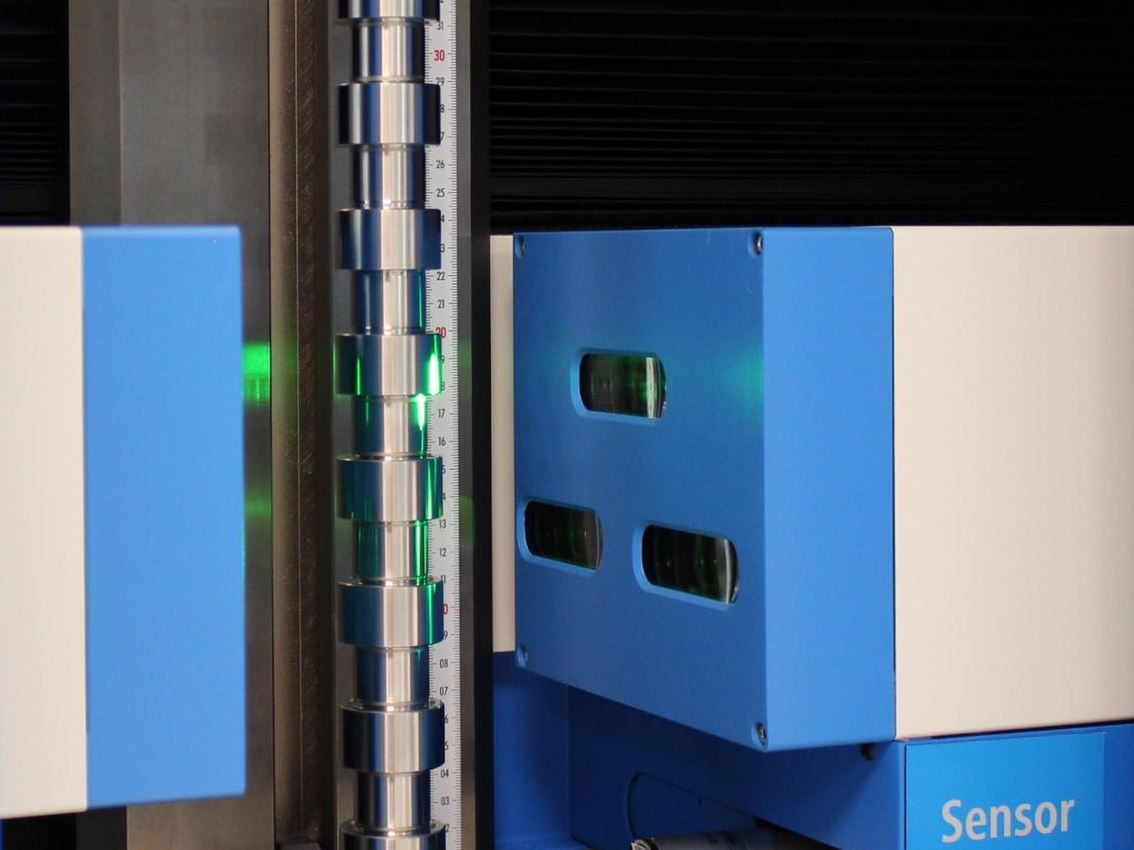
Collar shafts
- They are used to check or calibrate the longitudinal axis of the shaft measuring system
- There are two different diameters along the longitudinal axis
- A shaft represents several test lengths, the alignment of which is probed, bidirectionally on flat surfaces
- Measurement uncertainty is determined used synthetic reference data
- DAkkS-DKD calibration is carried out at an external calibration laboratory
Summary of standards and services
Visionline standards
Standards for calibration of optical inspection systems

Control rings are used to check and calibrate optical sensors for bore inspection (Visionline B sensors). Rings with a range of diameters are used according to the test diameter of the sensor: There are three sizes for Visionline B5, B20 and B100 sensors.
System control rings
- For regular calibration and system checks for light loss, lens soiling, etc.
- Each system control ring contains a number of different sized rings at a specific distance, which can be checked and evaluated
- The dimensional accuracy of the rings can be traced to national standards
- Calibration in an external calibration laboratory
- With a factory calibration report including specification for test uncertainties
Summary of standards and services
Calibration services for measuring devices
Roughness measuring devices
DAkkS-DKD calibration certificates for roughness measuring devices
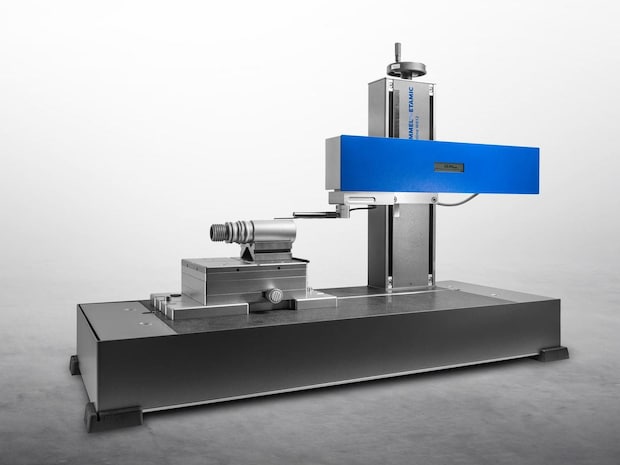
Requirements for roughness measuring devices using the profile method are high, as they measure roughness parameters of surfaces with different structures on different materials with a high level of measurement precision. Due to the large number of measuring systems that work in different ways, various DAkkS-DKD-certified standards are used for calibration.
- Calibration of the measuring system is usually done on site and ideally directly after a maintenance session
- Calibration according to ISO 12179 and the guideline of the German Accreditation Body DAkkS-DKD-R 4-2 Sheet 2
- According to the DAkkS-DKD procedures, only surface profilers with reference level probes can be DAkkS calibrated
- With a DAkkS-DKD calibration certificate
Summary of services
Optical shaft measuring devices
DAkkS-DKD calibration certificates for shaft measuring devices
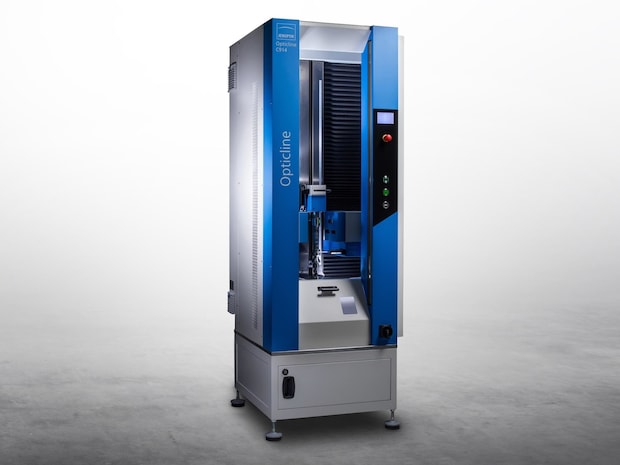
JENOPTIK Industrial Metrology Germany GmbH was the first DAkkS accredited DKD calibration laboratory for diameter and length measurements to be DAkkS-DKD-certified for optical shaft measuring devices in the Opticline series.
- Calibration of the measuring system is usually done on site and ideally directly after a maintenance session
- Calibration of the Opticline shaft measuring system by certified testers with DAkkS-DKD calibrated standards for the parameters diameter and length
- Calculation of the measurement uncertainty both from fixed components and from the current ambient conditions
- With a DAkkS-DKD calibration certificate
Summary of services
Standards, guidelines & literature
ISO/IEC 17025
DAkkS accredited DKD calibration laboratories are accredited in accordance with the global ISO/IEC 17025 standard. This standard defines the general requirements for competence, quality management systems, impartiality and uniform working methods of these laboratories to promote confidence in the measurement results of DAkkS-DKD calibrations. Each DKD calibration laboratory, therefore, works in accordance with the requirements of this standard.
ILAC
ILAC, short for International Laboratory Accreditation Cooperation, is an international association of accreditation bodies that also include ISO/IEC 17025 accredited calibration laboratories. It manages international agreements with these calibration laboratories in the fields of compliance assessment and creates the framework conditions for international exchange of calibration services.
An ILAC accreditation ensures global acceptance of accredited testing and inspection reports, calibration certificates and the results of qualification tests. The calibration laboratories are permitted to use the combined ILAC-MRA mark (Mutual Recognition Arrangement) on calibration certificates within the scope of DAkkS accreditation.
IATF 16949:2016
IATF 16949 is a quality management system standard (QMS) that lays down the basic requirements for quality management systems in the automotive industry. This QMS standard is not stand-alone; it is only used in conjunction with standard ISO 9001. It clearly states that only accredited calibrations are permitted whenever an accreditation exists for this parameter. Factory calibrations are not permitted in this case.
In chapter 7.1.5.3.2, the standard specifies which requirements external laboratories must meet so they can be permitted to provide testing and calibration services. They are:
- Accreditation in accordance with ISO/IEC 17025 or a comparable standard
- The calibration service must be included in the scope of the accreditation
- The calibration certificate must bear the accreditation mark of the national accreditation body
ISO 21920
ISO 21920 is a new series of standards in the field of roughness measurement technology. It updates and compiles a wide range of roughness standards (ISO 4287, ISO 13565, and others) and replaces them. It simplifies design specifications and can, if necessary, be specified according to function and production needs with a high level of flexibility.
Since, in practice, we will continue to work with the old profiles for a long time, they will remain for existing designs. Modifications and new designs should, however, be issued in accordance with ISO 21920. Modifications to most measurement conditions and roughness parameters are low. When referred to the calibration results of roughness standards, the calibration values only change very slightly, and lie for the most part within the specified measurement uncertainty. The Rmax parameter is replaced by Rzx; measurement conditions can be selected by configuration class; filter designations lc and ls become Nic and Nis.
The DAkkS accredited DKD calibration laboratory of JENOPTIK Industrial Metrology Germany GmbH has been accredited in accordance with the ISO 21920 standards series. This means you can choose according to which standards you wish your standards to be calibrated.
Roughness book
The reference book entitled Roughness Measurement – Theory and Practice gives a thorough overview of roughness techniques based on practice. Dr Raimund Volk, R&D Fundamental Research Manager at JENOPTIK Industrial Metrology Germany GmbH and author of the book, explains roughness parameters, describes the structure of surface measuring devices, helps users, and makes it easier for designers to specify surface parameters. The book is the ideal companion for all those who want to become familiar with roughness measurement.
PTB, DKD & DAkkS
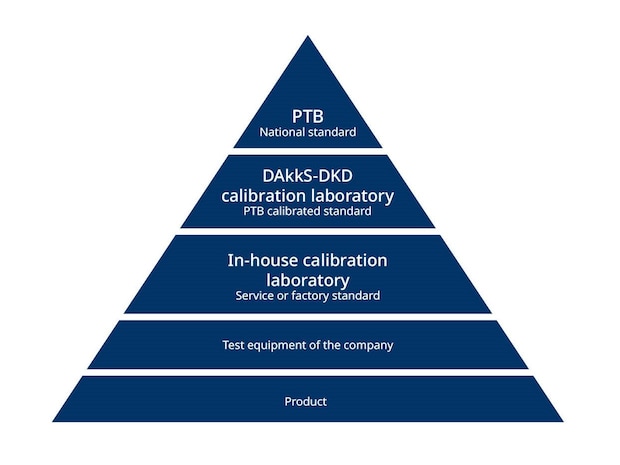
Calibration hierarchy
German National Metrology Institute (PTB)
The PTB in the national metrology institute of the Federal Republic of Germany. It is a research institute and higher federal authority of the Federal Ministry for Economy and Climate Protection that is responsible for measurement issues for science and economy. In Germany, the PTB is responsible for legally binding standards for measurement units that serve as a reference for any necessary calibrations.
The German Calibration Service (DKD) and the German Accreditation Body (DAkkS)
In the DKD, calibration laboratories of industrial companies, research institutes, technical authorities, monitoring and testing institutions founding merged when it was founded in 1977. On 3 May 2011, the DKD was re-founded as the technical committee of the PTB and accredited laboratories. This committee bears the name German Calibration Service (DKD) and comes under the aegis of the National Metrology Institute (PTB).
The guidelines and codes of practice drawn up by the DKD represent the state of the art in the relevant technical field and are available to the DeutschenAkkreditierungsstelleGmbH (German Accreditation Body DAkkS) for the accreditation of calibration laboratories. The accredited calibration laboratories are accredited and monitored by the DAkkS as the legal successor to the DKD. They carry out calibrations of measuring devices and measuring standards for parameters and measurement ranges stipulated in the accreditation. The calibration certificates issued by them are proof of traceability to national standards, as required by the ISO 9000 and ISO/IEC 17025 family of standards.
Source: Guidelines DKD-L 4-1 Test value uncertainty in the compliance assessment, edition of 04/2024, Revision 0, German Metrology Institute, Brunswick and Berlin. DOI: 10.7795/550.20240412
Glossary
Smallest measurement uncertainly possible
The smallest measurement uncertainty possible can be found in the DAkkS accreditation certificates of DKD calibration laboratories. The laboratory must not provide smaller measurement uncertainties for accreditation. The smallest available measurement uncertainty forms a benchmark for the performance of a laboratory.
The DAkkS accreditation of the calibration laboratory of JENOPTIK Industrial Metrology Germany GmbH demonstrates the following smallest possible measurement uncertainties:
- 12 nm
- 0.012 µm
- 0.000012 mm
- 0.000000012 m
That is 12,500 times smaller that the diameter of a human hair.
Duration of validation of the DAkkS accreditation
The regulations for the length of validity of a DAkkS accreditation have changed several times over the years. Since the judgment of the German federal administrative court (BVerwG) on the time limit of accreditations of 19 September 2018, accreditation certificates are issued without a time limit. They retain their validity until they are revoked, suspended, restricted or changed by the DAkkS, or the site renounces its accreditation.
The current status of the valid and monitored accreditation can be found in the database of accredited sites of the German Accreditation Body (www.dakks.de).
Time between each calibration
The frequency of calibration is not laid down, and each company must make their own decision on this. Factors such as the costs involved and the possible risk of incorrect measuring results must be borne in mind when making such a decision. The calibration laboratory or the manufacturer of the measuring systems offer a merely advisory role. This is because only the company knows which factors are relevant for making the decision. These may be frequency of use, place of use, test processes or the economic consequences of incorrect measurements.
Traceability
With the roughness, form, contour and shaft measuring systems from HOMMEL ETAMIC, an exceptionally wide range of parameter and characteristics can be measured. All these devices, however, have one thing in common: They measure lengths. To ensure that the values obtained with these measuring systems are also reliable and correct, they must – just like measurement means (standards) – be derived from all current quality standards (traceability).
The term traceability describes the process by which the measured value displayed by a measuring device or standard can be compared with the national standard for the measurement concerned in one or several stages. For HOMMEL ETAMIC, this means that all measuring instruments and standards must be compared with standards calibrated directly (or via several stages) by the PTB.
This ensures the connection to the International System of Units, shortened to SI (from the French: Système international d'unités). It is the unit system based on the International System of Quantities (ISQ). This was introduced in 1960 and is now the most used unit system for physical quantities in the world. To define the seven SI units (time, length, mass, temperature, etc.) as precisely as possible and to reproduce them, an attempt has been made to define all these quantities using an invariable natural constant.
JENOPTIK Industrial Metrology Germany GmbH's DAkkS accredited DKD calibration laboratory has standards for all accredited areas that have been calibrated by the PTB, and are, therefore, linked to and can be traced to the SI units via the PTB as the national metrology institute of the Federal Republic of Germany.
Example: History of the definition of "length"
- 1875 | At first, a meter was meant to be 40 millionths of the circumference of Earth
- 1889 | The Paris National Assembly ordered that a 1-meter-long rod of platinum-iridium be cast (original meter), but it was not accurate enough
- 1960 | The meter was defined as 1,650,763.73 times as the wavelength corresponding to the radiation propagated by atoms of the krypton isotope during their transition from the 5d5 state to their 2p10 state in a vacuum
- 1983 | A meter is defined as the distance that light travels in a vacuum in 1/299,792,458th of a second; the length is therefore defined by the natural constant of the speed of light c
Download the DAkkS accreditation scope
Questions about our products or our service? Our experts will be pleased to advise you!
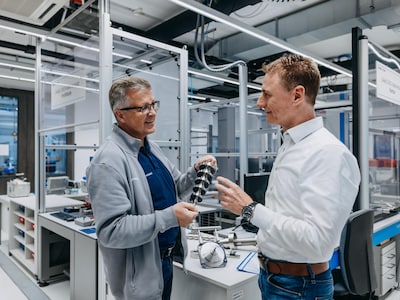
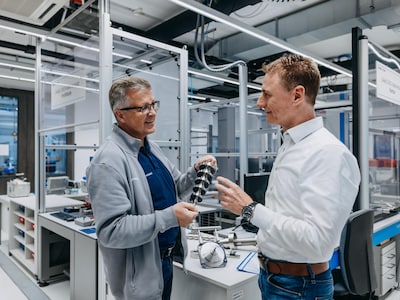
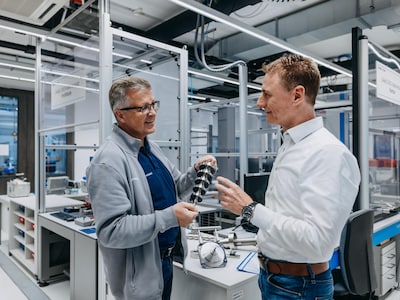
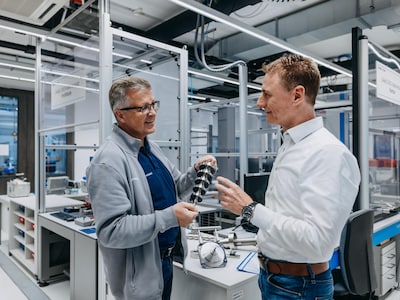
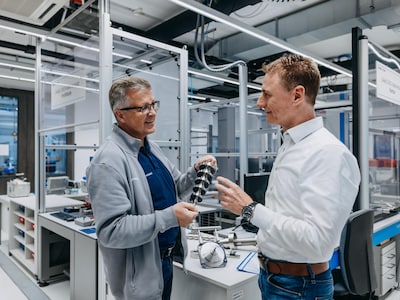
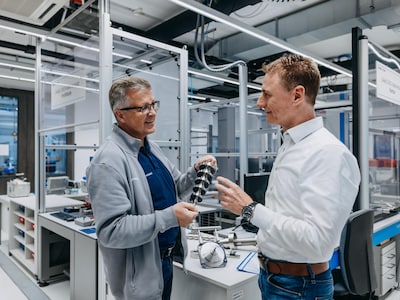
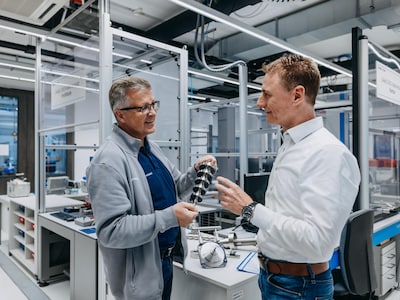
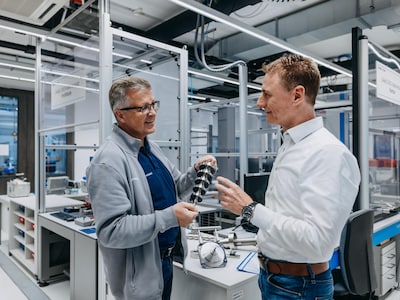
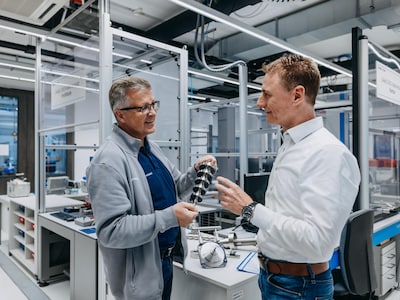
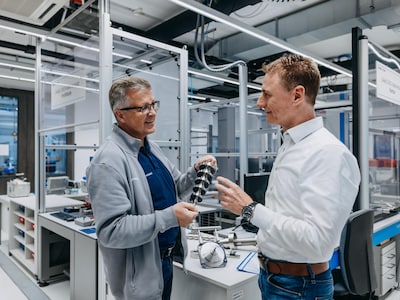
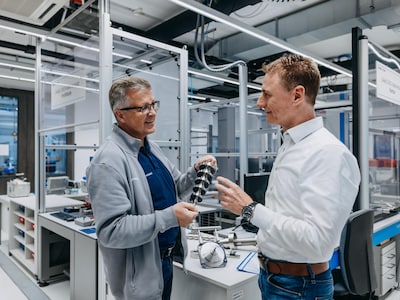
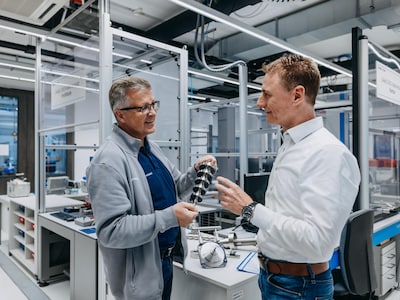
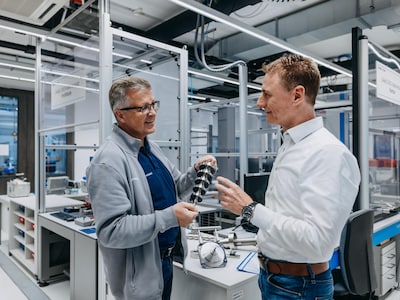
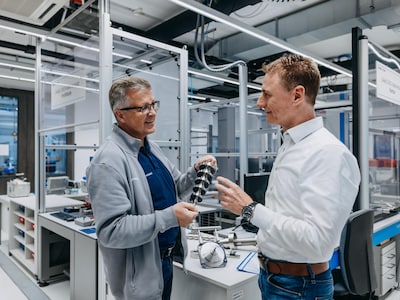
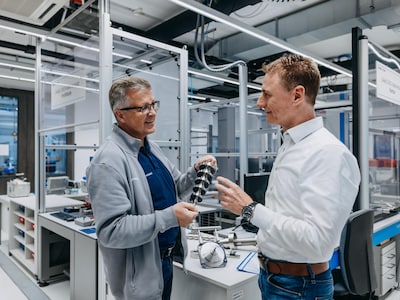
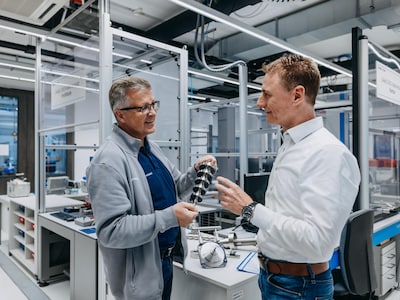
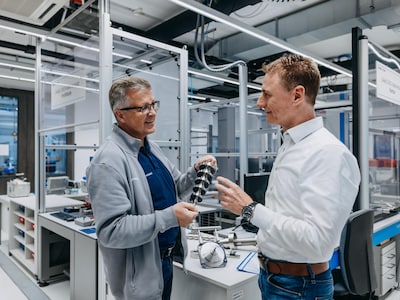
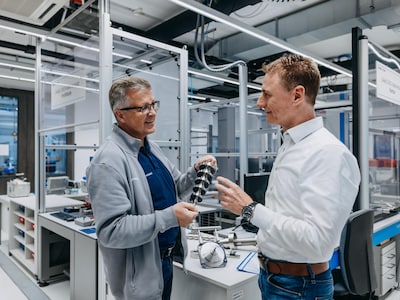
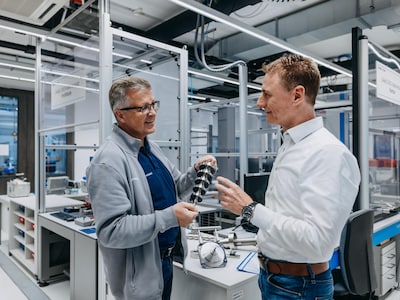
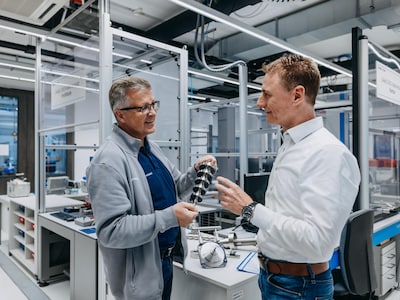
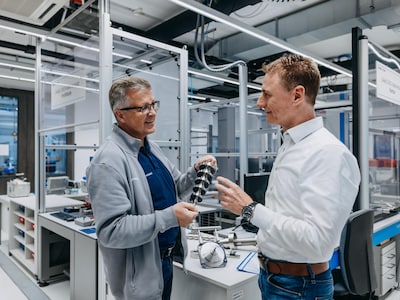
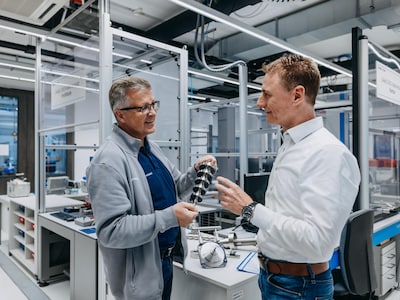
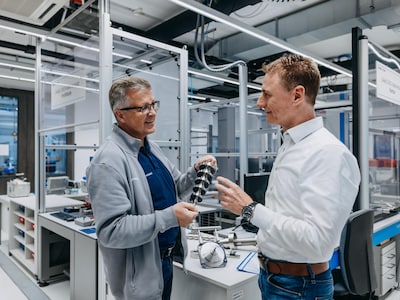
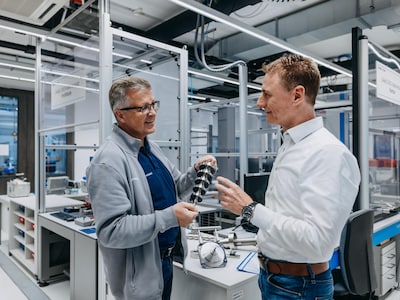
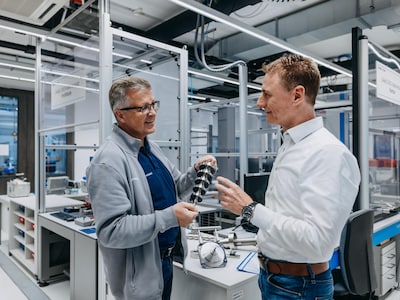
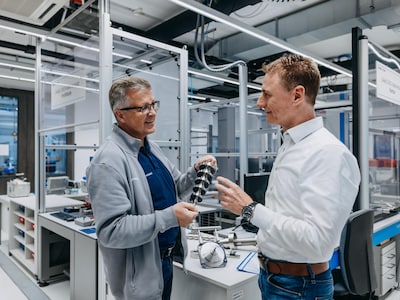
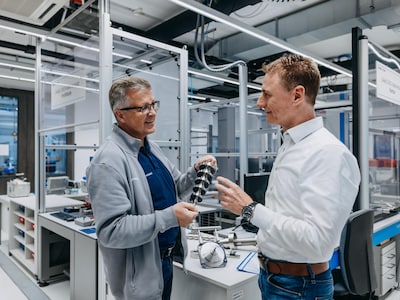
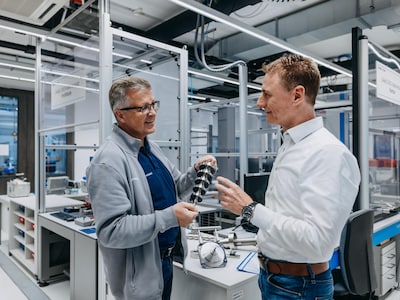
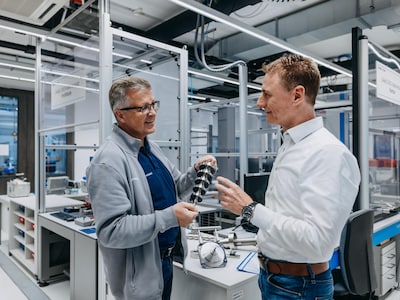
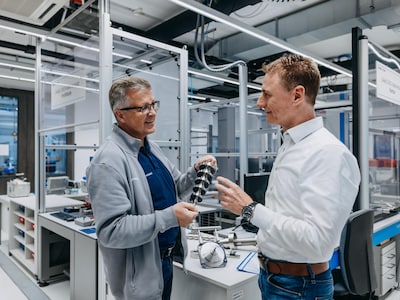
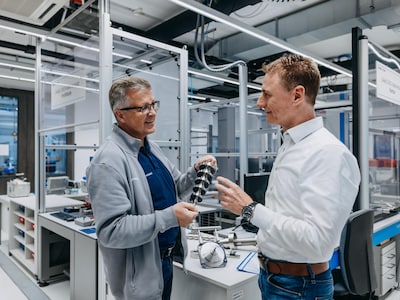